Winners Raise the (Adjustable) Bar for Construction Innovation
At the 85th Anniversary SCAL Annual Dinner in October 2022, three firms were felicitated for outstanding contributions to Productivity & Innovation in construction PIA Awards 2022. The Gold PIA was awarded to Welltech Construction Pte Ltd, Silver to Keller Foundations (S E Asia) Pte Ltd and Bronze to Gammon Pte. Ltd. & TTJ Design and Engineering Pte Ltd. Four very different awardees with different teams and different specialties but a common conjunction of best practices, attitudes, and mindsets that make for creative problem solving.
Solving problems on construction sites is not easy. With a dizzying number of moving parts, keeping things steady is already difficult and costly enough. Problems are simply an additional layer of pain and difficulty. But they are inescapable—in fact most of the construction profession can be described as fighting fires and keeping to plan. In confronting these fires, great steps have been made in the technologies that builders can employ as weapons: BIM has improved how projects are captured, from the big picture to intricate details; robotics and automation are changing the face of routine tasks. But the complexity and sophistication of these solutions are both the source of their power and the source of apprehension and even resistance by most contractors: innovation, it seems, is either too costly, too over-thetop, or too “cheem” for the average contractor; a big word found in seminars and in the verbal wallets of big firm executives, not on the ground and on the sites of regular contractors.
The winners of the 2022 PIA awards, who were chosen from a stable of applicants by appointed judges and in collaboration with SCAL’s Productivity & Technology Subcommittee, are the walking, talking evidence that the opposite is true:
innovation is not about budgets, it’s about budging; innovation can be found in big and small places and has much more to do with a firm’s mindset than costs and complexity.
AN ECONOMICAL AND EFFICIENT SOLUTION TO THE PROBLEM OF METAL DECKINGS FOR PPVC PROJECT
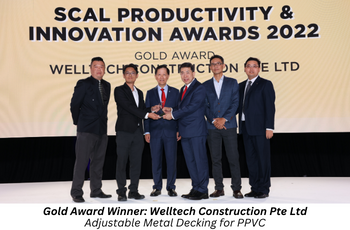
The Gold Award was awarded to Welltech for a solution whose simplicity is only matched by its profoundly positive effects for practically any project involving Prefabricated Prefinished Volumetric Construction (PPVC) today. Welltech’s team, led by Project Manager Maverick Lee and supported by Project Engineer Nikko Gozo, noticed that recycling metal decking from a previous project proved to be very costly in terms of time, energy, money, and space needed to modify the decking to fit the dimensions of the new project. Modifying existing decking is difficult work that can also add unnecessary risks to the project site. Often, making these modifications can costs as much as procuring new decking, and with tight project deadlines, contractors are caught between a rock and a hard place: waste previous decking by fabricating anew, or modify and waste time and effort—both at the same cost.
Welltech’s team decided to confront this head on. After a brainstorm, it became clear that slotting or telescoping might be a promising way to make the deckings adjustable, and so more easily reusable project to project. Two designs were settled on—one based on plates and the other on hollow slots—before Welltech’s team came together to evaluate and settle on one. And here collaboration was key: the on-site team came back with feedback on the recesses at the end of the metal deck, the Professional Engineer (PE) offered calculations on structural integrity, and the steel fabricators offered advice on the workability of their design.
A prototype was assembled, but only after a fair wait. Pressure was on and nervousness set in—the team was confident that their prototype would stand the test (literally). But if they failed, on-site progress would grind to a halt. “We were taking a risk with this new solution,” Maverick said, “if it didn’t work out, we would have to rush to get the right metal decking to avoid delays on site.” Nikko added: “There was definitely a lot of pressure because we were exploring this solution in parallel to our regular site work.”But it paid off, and Welltech’s solution was successfully installed at their project, setting a foundation for future projects as well. The team expects that 4- or 5-sided precast modules, such as those used by HDB, would benefit from this stackable, modular solution.
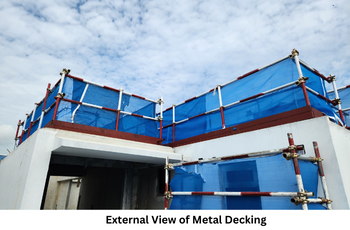
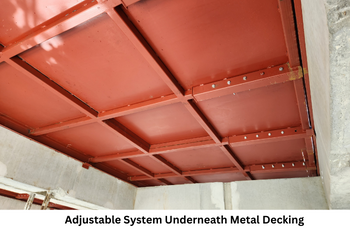
REMOTE-CONTROLLED AIR-HAMMER OPERATION
And regarding foundations, digging deeper to lay them is what Keller Foundations—the Silver PI
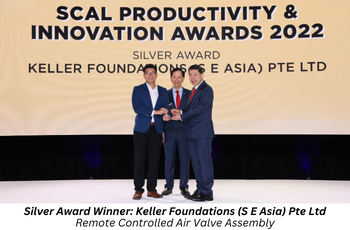
A awardee and a geotechnical contractor— must
reckon with every single day. Drilling and piling work require the use of an air- pressure-operated Down the Hole (DTH) hammer, often without alternatives since the next best thing (a water hammer) is weaker and unacceptably polluting. DTH hammer work involves many extremes: of pressure, of temperature, and of noise. The operator of the DTH hammer’s air compressor must face all of these while also being in the line of fire of the air pressure hoses.. Communication errors are also rampant as other team members need to shout over the great noise to pass instruction to the operator. Unsurprisingly, a 2020 internal analysis of near misses and site hazards found that air hammers accounted for 20 near-misses—a high number compared to other sources of nearmisses.
So, Keller’s team, led by Deputy Project Manager Wong Jian Wen and supported by Senior HSEQ Executive Phyo Thiha Aung, set out to support their on-site staff and make DTH hammer air compressor operation safer and more efficient. Three teams—the safety team, the operations team, and the mechanical (yard) team—put heads together.
Since most other options such as water-powered DTH hammers were easily eliminated (on grounds of site feasibility and productivity), it became evident that automation of the DTH hammer air compressor unit was the way to go. But asking the manufacturer to make the equipment fully remotely controllable would be too costly as well since there are only so many DTH hammer compressors to procure in the market.

Keller’s team therefore decided to take the DTH hammer compressor in their own hands: they would develop remotecontrolled valves as a brilliant midway solution between full remote and manual operation of the equipment. The mechanic team sourced the hardware but the individual components of their remote-controlled valve (the wires, the bulbs, etc.) were all individually sourced by the team and then assembled. A prototype came together, and the team learned that it worked better than expected—remote valve control from greater than a Kilometer away. But the team also learned that the prototype needed to be refined to show equipment status to the remote operator.
Exceeding expectations, Keller’s remote-controlled compressor valve had several important benefits: apart from the obvious improvements of safety outcomes, the solution proved to be practical in its ease of installation, use, and maintenance, and reduced the footprint of the air hammer in sites that often have scarce laydown space.
MODULAR CLIMBING BRACKET SYSTEM
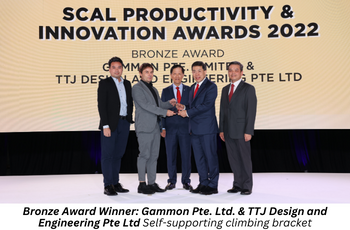
The Bronze Award was awarded to Gammon & TTJ Design and Engineering for a solution that started from simple first principles but built atop itself (not just figuratively) to produce a complex solution. Faced with a very tight project laydown area that would have certainly been choked by hefty temporary works and a precast, modular structure, Gammon’s team— led by General Manager Michael O’Connell and supported by Raymond Ngiam—thought to get two birds with one net. By exploiting the repetitive and modular structure of the structure, Gammon developed a similarly modular and repetitive bracket that, like a vine, climbed with the structure as it installed additional layers.
What started with a hand sketch with Gammon’s cooperative specialist contractor TTJ Design and Engineering was then translated to BIM before a virtual installation using the BIM model. It was the model that then validated the initial idea.
Finally, a prototype, many shop drawings, and some lessons later, Gammon’s climbing bracket finally began to come together and materialize on the actual project site. Benefits included less steel, less labour, and less time - and so less cost.
3 LESSONS FROM THE WINNERS REGARDING CONSTRUCTION INNOVATION THAT ALL CONTRACTORS CAN TAKEAWAY
Lesson 1: Resistance to change must be expected and planned for
The first is that resistance to change must be expected and planned for. Jian Wen from Keller shared, “Inertia is a major factor. The longer the team does the same thing, the harder it is to change. The best time to change was five years ago (since change takes time to bear fruit). The second-best time is today.” Michael from Gammon also resonated with that challenge. “There was a lot of scepticism, to be honest. There’s always a level of disbelief when something bespoke without precedent is done.” In Gammon’s case, this disbelief (potential and actual) came from many quarters: the site team, the consultants, regulators such as BCA, and management. “Internal scepticisim was stronger than external scpeticism,” Michael added. But both Gammon and Keller converged on the same solution to suspending this disbelief and inspiring confidence: get it done, and they will come round. Through mockups, prototypes, and demonstrations, both firms were able to overcome doubt that often paralyses innovation at other construction firms.
Keller additionally overcame one of the greatest sources of doubt—cost—by reasoning out a business case for their proposed remote-controlled valve. By demonstrating clear financial costs and benefits, time-to-profit, and break-evens for the solution without feeling intimidated by the upfront cost, Keller overcame the inertia that often sets in when a good idea is given a price tag. Gammon overcame another key doubt—safety—by adhering to its robust internal practice of Zero Harm presentations to management.
Lesson 2: Innovation is impossible without collaboration and, importantly, the blessing of management
The second lesson is that innovation is impossible without collaboration and, importantly, the blessing of management. A collaboratively innovative culture doesn’t grow overnight. It needs tending to, nurturing leadership, and a transparent environment. Gammon is a leader in this field, with an established practice of using BIM early in its construction methodology as well as an initiative to have site teams use SketchUp to develop and implement their own solutions. But this outlook isn’t just for the bigger fish.
Keller has broken down the siloes between its departments—on-site and in the office—and hosts an annual Continuous Improvement and Innovation Day (CIID), where the whole company takes a day off, books a seminar room, and works towards bettering themselves individually and as a firm— from engineering to finance. Sometimes, the empathy cultivated from a collaborative environment is enough to trigger innovation. “I always put myself in the workers’ shoes,” Jian Wen from Keller said, “If I’m able to do what they’re doing then okay but if I can’t then I need to come up with a better way. If we take them for granted, we won’t realise there’s a problem, and so innovation can’t happen.”
Strong and committed leadership is necessary to set up and then sustain such an environment while balancing healthy risk-taking with the best interests of the firm. Keller and Welltech both concurred that a supportive and open-minded management buoyed their innovation successes. In Gammon’s case, Michael was the management but found support from his colleagues both above and below.
Welltech’s Maverick and Nikko said that success for their team came from believing in their team and not backing down in the face of adversities, but also depending on partners across the project value chain—from suppliers to experienced fabricators. Gammon’s project was so indebted to a strong relationship with a specialist subcontractor that it shared the award with Gammon, said that having a specialist subcontractor willing to take an off-the-wall idea and turn it into reality gives hope for innovation. Most subcontractors simply do not bite this bullet. “The most pleasing thing was that, while others might say that the idea was silly, the subcontractor took it at face value, developed it, and ran with it.”
Lesson 3: Open mindedness must be enhanced with open data
Finally, the third lesson is that open mindedness must be enhanced with open data. All three sets of awardees used BIM or other datadriven technologies for their solutions—Gammon to develop the design and simulate installation, Keller used self-sourced hardware and communications technology, and Welltech used BIM for shop drawings.
Technology is essential as a bedrock on which can rest excellent collaboration and transformation. The 2022 PIA winners have made a mark in the sand of construction innovation in a period of great change for the construction industry.
The article is extracted from The SCAL Contractor Newsletter - issue 3. Read the full issue in the link here or click here to download.